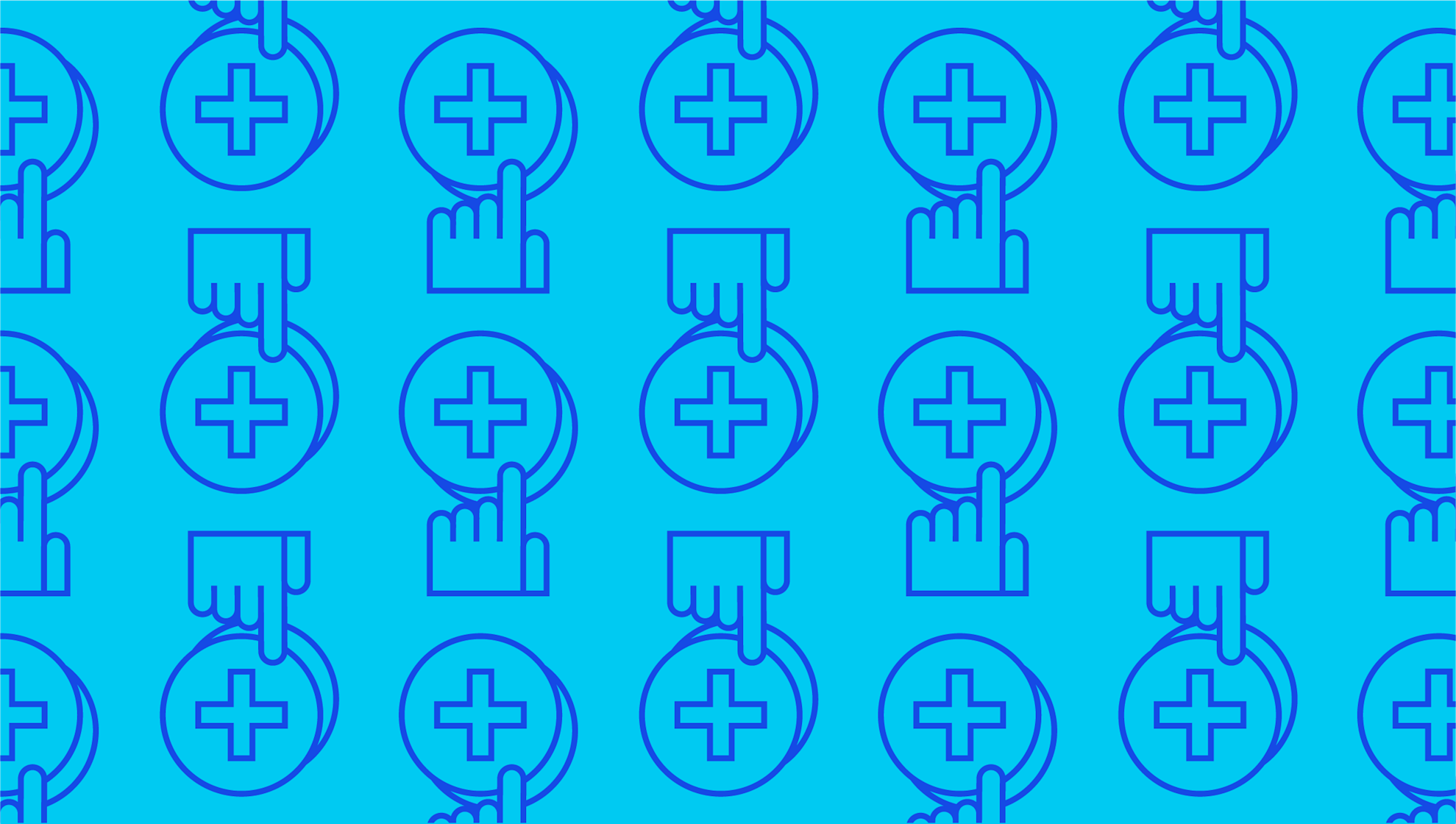
Total Quality Management (TQM): A Complete Guide
Last editedJan 2021 3 min read
Total quality management is a management system that focuses on producing the highest quality product or service. It aims to ensure maximum customer satisfaction and promote the long-term success of a company.
Total quality management definition
There is no formal definition of total quality management. There is, however, a definition of the steps involved in quality management. These are:
quality planning
quality assurance
quality control
quality improvement
Quality assurance and quality control are similar but different. Quality assurance is essentially about preventing defects. Quality control is about making sure that the product or service meets the accepted standard.
Hence the practical definition of total quality management is essentially managing all of these steps with a focus on maintaining the highest possible level of quality throughout the entire process.
Total quality management principles
There is no formal, centralised document repository for total quality management the way there is for related management frameworks such as ISO. This means each organisation is free to adopt it and adapt it in the way that best suits their business.
There are, however, a couple of standard reference points that are incorporated into most implementations of TQM systems. Both come from W Edwards Deming. The first, and simplest, is the Deming cycle. This is Plan > Do > Check > Act.
For start-ups and smaller companies, keeping this basic cycle in mind may be enough to guide a total quality monitoring approach. The more detailed reference point is Deming’s 14 points for management. These are not specific to total quality management, but they do act as a frame of reference for it.
Over the years, Deming’s list has been streamlined and summarised into the following key points.
Customer satisfaction
Everything an organisation does should contribute to attaining the highest possible standards of customer satisfaction.
Continuous improvement
Every last person in a company, at all levels, should be empowered and encouraged to look for ways to improve how the business performs its operations.
Effective communications
If everyone has to pull together towards a common goal, then, at the very least, everyone has to know what that goal is and how they are expected to contribute to it. This means that it is vital to have effective communication in and between all levels of a company.
Integrated systems
All internal systems should work holistically rather than in silos. This doesn’t mean all employees need to have access to all data. Quite the opposite, this would probably bring about overload. It would also probably be a serious breach of data privacy laws. It simply means that systems need to facilitate teamwork rather than act as a barrier to them.
In some cases, it may be appropriate to include external stakeholders in company systems. For example, suppliers’ systems may interface with the customers. Similarly, end-customers may want a straightforward way to communicate with the company.
Process-oriented
In simple terms, you break each task down into its component processes. Then you discard any unnecessary processes and hone the ones that remain. Any processes that survive the cut at any given point in time may still be discarded later.
Data-driven decisions
It’s probably not a coincidence that total quality management emerged about the same time as modern IT. Even in its early days, total quality management often made use of robust statistical analysis. As computing power has grown, so have the options for making data-driven decisions.
Strategic thinking
Total quality management is fundamentally all about improving processes, but processes only have meaning when they are part of a strategy that leads to a vision. Ultimately, creating this strategy is down to management, but all employees can contribute.
Total quality management advantages and disadvantages
Properly implemented, total quality management leads to a company getting maximum results at minimum cost. This means satisfied customers and engaged employees.
The disadvantages hinge on the fact that it is a labour-intensive process and often requires upfront investment. It may also be difficult to gauge the return on this investment. For example, in the early days of implementation, a company may see a marked decrease in certain costs. These can include appraisal costs, prevention costs and failure costs (both internal and external).
Over time, however, total quality management will typically become more about maintenance and incremental improvements than significant upgrades. At that stage, it may become harder to see the link between the cost of implementing total quality management and the cost savings made as a result.
Total quality management examples
Total quality management is intrinsically associated with the economic revival of Japan after WWII. It also played a large role in revitalising US industry in the 1970s and 1980s.
Since then, total quality management has been increasingly superseded by ‘descendent’ frameworks. These include Six Sigma, lean management and ISO. Some major companies, including Toyota and Tata Steel, still lean heavily on total quality management.
How we can help
If you’re interested in finding out more about total quality management (TQM), then get in touch with the financial experts at GoCardless. Find out how GoCardless can help you with Ad hoc payments or recurring payments.