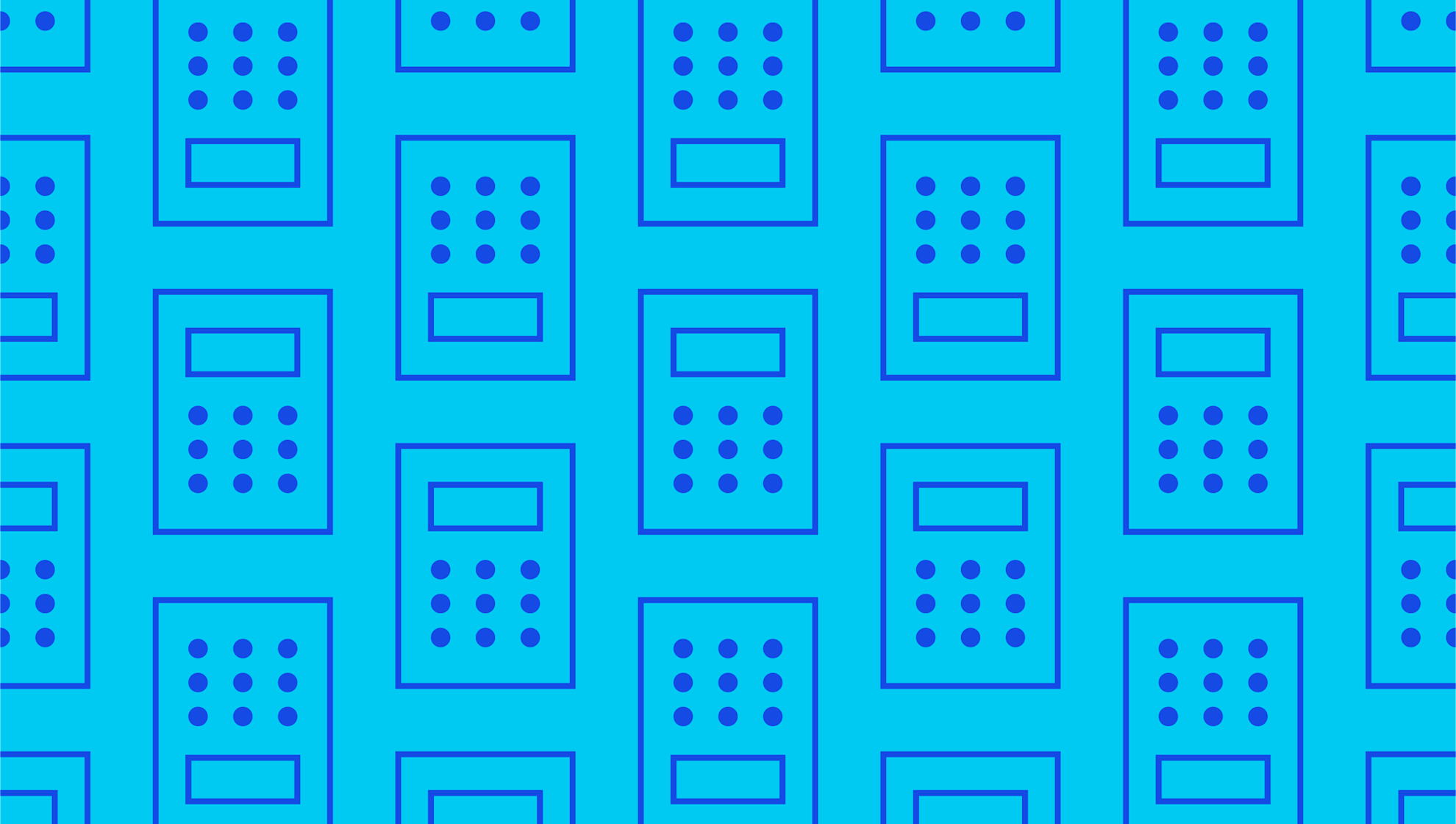
What Is Activity-Based Costing (ABC)
Last editedJune 2021 3 min read
For businesses, selecting the right price can be a delicate balancing act. On the one hand, you want to attract customers with a price low enough to purchase your goods and services. On the other, you need to cover your operating costs and make a sustainable profit. One approach that can be helpful is activity-based costing (ABC). So, what is activity-based costing and how does it work? Let’s take a closer look below.
Activity-based costing definition
Activity-based costing (ABC) is a method used in business to assess the cost involved in production. It assigns both overhead and indirect costs to their related services or products, so that you can figure out exactly what it costs to get each product onto the shelves. While this ABC method management accounting formula is applicable to any industry, it’s primarily used in manufacturing.
By looking over all overhead activities involved in the production process carefully, you can formulate a more accurate pricing model than with some other costing methods.
What is activity-based costing and how does it work?
The purpose of the ABC costing method is to break down each manufactured item into easily classifiable data. You can do this by identifying all the specific related costs and analysing their drivers. It’s used not only in company pricing strategies, but also in profitability analysis to see if your margins are where they should be.
There are many different tasks associated with production, including processes like setting up machines, distributing goods, and designing new products. Each of these tasks consumes a certain amount of overhead, whether it’s electricity for operating machinery or Wi-Fi for accessing computer programs. Generally, the ABC costing method breaks down manufacturing into five main levels of activity:
Batch-level
Unit-level
Customer-level
Organisation-level
Product-level
One of the key points to understanding ABC costing is that while customers and products consume activities, activities use up resources. Therefore, resources should be allocated to those activities that will generate the most profit.
ABC cost drivers examples
There are many different types of activities that qualify as cost drivers in manufacturing. Here are a few typical ABC cost drivers examples to include:
Number of machine hours
Number of labour hours
Numbers of packed orders
Number of delivered orders
Number of completed orders
How to use activity-based costing
If you were to break down ABC costing into a simple formula, it would take the cost pool total and divide it by the cost driver to obtain a cost driver rate. This is then used to calculate all indirect and overhead costs related to any specific activity. Here’s a step-by-step process:
Take note of all activities related to the production of your service or product.
Divide these activities into cost pools and calculate the total overhead cost for each pool.
Assign appropriate cost drivers to each cost pool activity.
Divide the cost pool total by the cost drivers to obtain the cost driver rate.
Multiply this rate by the number of cost drivers.
For example, imagine that Company XYZ has an annual electricity bill of $25,000. A cost driver that directly impacts this bill is labour hours. If there were 5,000 labour hours worked during the year in question, you could calculate cost driver rate by dividing the $25,000 bill by 5,000 hours to yield a cost driver rate of $5 per labour hour.
Now imagine that Company XYZ uses 5 hours of electricity to produce each product. Multiply this by $5/hour to determine that the overhead costs will be $25 in electricity. You would then repeat the process with each overhead cost.
What are the benefits of Activity Based Costing (ABC)?
The ABC method of management in accounting offers some distinct advantages.
It breaks cost down by activity for an accurate overview, allowing businesses to implement smarter pricing strategies.
It helps identify more profitable activities so you can properly allocate resources.
At the same time, there are also some limitations to be aware of:
If your company’s products or services don’t use up many resources or overhead costs, it may not be as accurate.
Not all costs can be assigned to clearly defined activities.
For those in manufacturing, ABC costing is an effective strategy to managing pricing. Yet for those with a higher degree of indirect costs, it may not be as efficient. It’s best to use several pricing models to understand the true cost of goods sold.
We can help
GoCardless helps you automate payment collection, cutting down on the amount of admin your team needs to deal with when chasing invoices. Find out how GoCardless can help you with ad hoc payments or recurring payments.